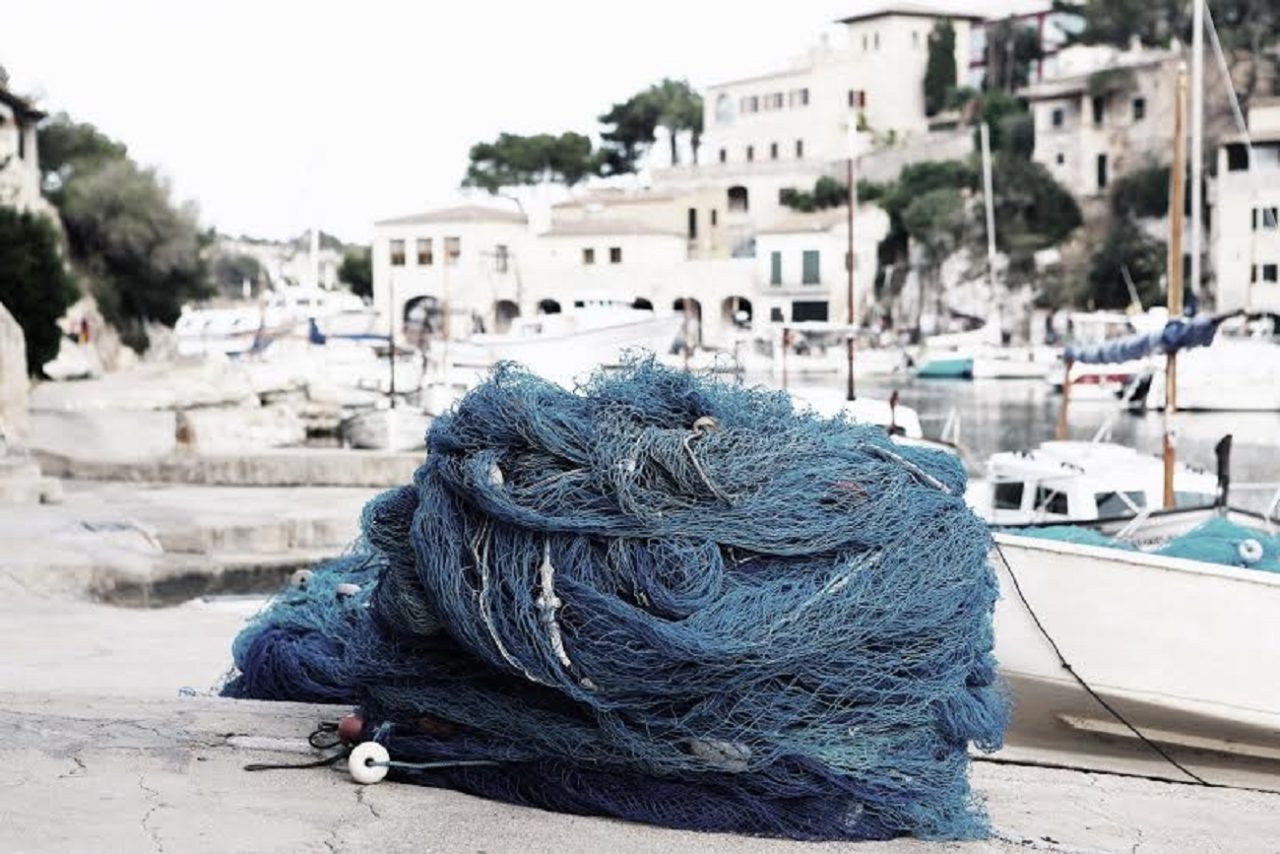
L’idea sembra semplice e virtuosa: usare il nylon, soprattutto quello presente nelle reti da pesca, per dare vita a nuovi prodotti, dagli skateboard agli occhiali da sole ai tessuti sintetici per gli indumenti sportivi. Ma a rendere tutto più complicato è il lungo processo che sta dietro alla lavorazione e al riciclo del nylon, uno dei materiali più inquinanti e meno eco-sostenibili in commercio.
Un’invasione di nylon nei nostri mari
Il nylon, una fibra sintetica composta da polimeri messa in commercio nel 1939 a New York, si espanse in particolare dopo la fine della Seconda guerra mondiale. Fino a quel momento, infatti, cotone e lana erano i must nel mercato dei tessuti. In poco tempo i tessuti sintetici, e tra di essi il nylon, conquistarono buona parte di tale mercato arrivando presto ad una quota pari al 25%. Il nylon, usato inizialmente come filamento per i vestiti delle donne, divenne fondamentale anche per altre industrie, come ad esempio quella militare, in particolare nella produzione di prodotti come tende, paracaduti, e uniformi, e quella ittica, per la realizzazione delle reti da pesca. Da tempo ormai sono proprio tali reti uno dei più grandi elementi inquinanti degli oceani. Secondo un rapporto della Fao e dell’Unep, l’agenzia delle Nazioni Unite per l’ambiente, ogni anno sui fondali marini e oceanici sono abbandonate dall’industria ittica circa 640mila tonnellate di reti da pesca per una percentuale che arriva al 10% del totale dei rifiuti solidi. Nelle acque profonde del Nord-Est dell’Atlantico, ad esempio, ogni anno risultano perse circa 25mila reti, che coprirebbero una lunghezza pari a ben 1.250 km. Ogni rete è in realtà una vera e prora trappola mortale galleggiante. Alcuni ricercatori statunitensi hanno stimato, per esempio, che una singola rete fantasma può uccidere, nell’arco di 10 anni, una quantità di granchio Granciporro pari a quasi 20mila dollari di valore. E ancora, quando 870 reti fantasma sono state recuperate al largo dello stato di Washington esse contenevano più di 32mila animali marini, tra i quali più di 500 uccelli e mammiferi. Anche Heather Koldewey, direttore dei programmi internazionali di conservazione della Zoological Society London, dimostra con altri dati l’imponenza e l’urgenza del problema. Un peschereccio industriale di grande pescaggio, attrezzato nel modo più tecnologico per la cattura, è talmente grande che potrebbe ospitare nella sua stiva 13 jumbo jet. Questo tipo di imbarcazioni cambia le reti ogni due o tre mesi: quelle vecchie vengono gettate in mare. “Si calcola che per ogni chilo di plancton ne esistano sei di frammenti sintetici non biodegradabili – spiega Koldewey – e che per ogni chilometro quadrato di oceano ci siano 30mila pezzi di plastica”. Ancora più preoccupante lo scenario descritto da Francois Galgani, biologo francese tra i più esperti dell’Ifremer francese e Advisor del network internazionale Plastic Oceans, che spiega molto bene l’inquinamento derivante dai piccoli frammenti nei quali i vari tipi di plastica, tra i quali il nylon, si rompono: “I frammenti di plastica traghettano batteri e vibrioni, patogeni potenzialmente pericolosi per gli ecosistemi. Sono in grado di spostare specie non autoctone dal Giappone al Canada affidandosi alle correnti oceaniche. Stiamo quindi parlando di un inquinamento micro-organico da specie invasive”. Un riciclo complicato ma virtuoso
A complicare le cose c’è la difficoltà di recuperare le reti dalle profondità degli oceani e poi quella di riciclare tale materiale. Stephen Johnston, professore associato di ingegneria plastica presso l’Università del Massachusetts Lowell, sostiene infatti che “dopo averla trascinata con una barca dal fondo dell’oceano, la rete risulta molto difficile da pulire prima che possa essere riciclata”. Il problema è quello legato alla contaminazione. A differenza dei metalli e del vetro, che vengono fusi ad alte temperature, il nylon viene fuso a una temperatura più bassa. Così alcuni contaminanti – come elementi non riciclabili e microbi o batteri – riescono a sopravvivere. Questo è il motivo per cui il nylon deve essere pulito a fondo prima ancora che il processo di riciclo abbia inizio.
Negli Usa una nuova primavera per il nylon riciclato
Così, tre anni fa, tre amici di Los Angeles, David Stover, Ben Kneppers and Kevin Ahearn, decidono di lasciare il loro lavoro e fondare la Bureo, una società che oggi si occupa di realizzare skateboard e occhiali da sole con nylon riciclato. Come ricorda Stover, l’idea nacque dall’osservazione di quanta spazzatura fosse dispersa nel mare. “Quando abbiamo provato a capire quali fossero i rifiuti presenti nell’oceano – sostiene – abbiamo appreso che esiste un flusso costante di reti da pesca in nylon oggetto di abbandono in mare ogni anno, reti che possono restare lì per generazioni. Questo è infatti un materiale che non si rompe”. Oggi l’azienda paga pescatori in Cile per raccogliere le vecchie e abbandonate reti da pesca in nylon per poi sottoporle a un lungo processo di riciclo e trasformarle in skateboard e occhiali da sole. Negli Stati Uniti molti altri brand stanno scegliendo di utilizzare nylon riciclato per le loro produzioni, dalla società Outerknown di Los Angeles, specializzata nel realizzare abbigliamento sportivo da esterni, al gigante dei costumi da bagno Speedo (con il tessuto Powerflex Eco) alla californiana Patagonia, che oggi produce una cinquantina di prodotti contenenti nylon riciclato in diverse percentuali (il loro giaccone Torrentshell, ad esempio, è fatto al 100% con nylon riciclato).
Dall’Italia arriva il processo di riciclo del nylon
Tutte queste realtà si stanno sviluppando negli Stati Uniti, grazie anche alla maggiore attenzione che sempre più i responsabili delle aziende di tessuti stanno prestando alla eco-sostenibilità dei loro prodotti. In realtà, però, un altro punto in comune tra tutte queste imprese si trova nel nostro Paese. Si tratta dell’azienda manifatturiera Aquafil, prima realtà nel mondo ad avere studiato per anni il nylon e ad averlo utilizzato come prodotto riciclato. È stato così inventato il brand Econyl, che l’azienda italiana ha poi venduto anche ai grandi colossi americani. Secondo Giulio Bonazzi, Ceo del gruppo Aquafil, “l’essenza di Econyl sta proprio nel ridurre progressivamente la quantità di rifiuti del nostro pianeta, recuperandoli e rigenerandoli, per inserirli nuovamente nel ciclo produttivo, quali materie prime di qualità con caratteristiche pari al prodotto vergine”. Il processo seguito, chiamato Econyl Regeneration System, è piuttosto lungo e complicato, ed è suddiviso in sei step. Prima di tutto si recupera il materiale, quindi il nylon, in località differenti, sparse in tutto il mondo. Nelle sedi di raccolta vengono radunati prodotti alla fine del loro ciclo di vita, come le reti da pesca, i tessuti e il fluff proveniente dalla pavimentazione tessile. Particolari collaborazioni sono attive in paesi come Canada, Stati Uniti, Grecia, Egitto, Pakistan, Turchia, Tailandia e Norvegia per recuperare vecchie moquette e tappeti. Tutto il materiale viene poi inviato al centro di raccolta e trattamento di Ajdovščina in Slovenia. Qui i diversi materiali vengono puliti e preparati per la depolimerizzazione. In questa fase di pulizia, i materiali differenti dal nylon 6, come rifiuti organici, plastica o elementi metallici, vengono divisi e inviati in altri stabilimenti di smaltimento. I rifiuti di nylon ripuliti sono poi triturati, compattati e imballati, per essere trasportati all’impianto di rigenerazione Econyl della vicina Ljubljana. Nella depolimerizzazione il nylon viene sottoposto a una decomposizione idrolitica che isola il caprolattame, un derivato della nafta, e quindi del petrolio, che è l’ingrediente di base del nylon stesso. A questo punto si procede ad una nuova polimerizzazione. Il caprolattame che viene prodotto possiede le stesse caratteristiche chimiche e prestazionali di quello proveniente dalle materie prime fossili. Il processo chimico e i metodi di trasformazione del caprolattame Econyl in polimeri di nylon 6 è quindi identico al processo di polimerizzazione del caprolattame vergine. I polimeri di PA6 prodotti da caprolattame Econyl sono distribuiti nei vari impianti di produzione, dove vengono trasformati in filo Bcf (per pavimentazione tessile) e filo Ntf (per tessili e abbigliamento). Infine i nuovi fili Econyl saranno poi usati per produrre manufatti destinati a diversi mercati finali. Per fare degli esempi, per ogni tonnellata di reti da pesca recuperate e rigenerate viene prodotta una quantità di filo utile a più di 26mila paia di calze, supponendo una percentuale di Econyl nelle calze del 50%, e a più di 1.000 metri quadrati di tappeto, calcolando un tappeto di 600g/m2.